Table of Contents
Automatic sheet metal bending refers to the use of automated equipment (such as CNC systems, servo drives, robotic arms, etc.) to automatically complete the bending process of sheets or metal workpieces.
This process no longer relies on manual operation, but achieves efficient, accurate, and repeatable bending through preset programs and mechanical actions. It is one of the core technologies for modern sheet metal processing and intelligent upgrading of manufacturing.
1. What is automatic sheet metal bending?
Automatic sheet metal bending refers to a processing method that uses automated equipment (such as CNC press brake machines, bending robots, automatic bending centers, etc.) to accurately bend metal sheets to achieve the desired shape.
It is an upgraded version of traditional manual bending, relying on program control and automatic execution to achieve high-efficiency and high-precision sheet metal processing.
Core Principle
Automatic bending usually includes the following steps:
- Loading: A robot or manipulator feeds the sheet into the equipment;
- Positioning: The system automatically identifies and adjusts the position of the sheet;
- Bending execution: The bending tool is controlled by CNC to complete the bending according to the angle and pressure set by the program;
- Unloading/stacking: The folded workpieces are automatically fed out or stacked in categories.
Typical equipment included
- CNC Press Brake: The bending action is driven by CNC program, and some manual loading is done.
- Bending Robot System: Cooperate with the robot arm to realize unattended bending.
- Automatic Bending Center: From loading to bending to discharging, all are completed automatically.
Applicable materials
- Stainless steel plate
- Cold-rolled steel plate
- Aluminum alloy plate
- Galvanized plate
- Copper plate and other metal thin plates
The thickness is usually between 0.5mm – 6mm, depending on the equipment specifications.
2. Advantages of automatic sheet metal bending
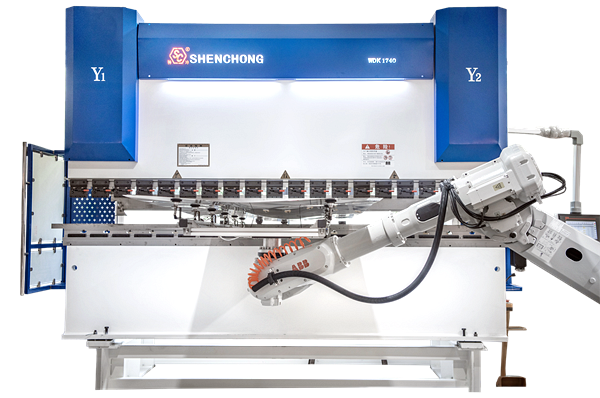
Automatic sheet metal bending technology has significant advantages and characteristics in modern manufacturing. The following is an analysis of its main advantages and characteristics.
1) Significantly improved production efficiency
Automatic loading and unloading system:
Automated bending equipment can be equipped with mechanical arms, suction cups, and conveyor lines to achieve automatic loading, alignment, bending and unloading of sheets without manual intervention, greatly reducing process conversion time.
Multi-process integration:
Automatic bending centers often integrate pre-bending, mold changing, indentation, unloading and other functions in one, completing multiple processes on the same workbench to shorten the total production cycle.
High-speed operation capability:
High-performance servo motors and CNC systems work together to ensure precise control during high-speed movement, greatly shortening the processing time of a single piece, and are suitable for large-volume orders.
2) Significantly improved processing accuracy and consistency
CNC precision control:
Bending angle, position, pressure and other parameters are input through the CNC system, and the accuracy can usually be controlled within ±0.1mm, and the angle error can be less than ±0.3°.
Compensation system support:
Automatic bending machines are often equipped with angle detection and deflection compensation systems, which can monitor the rebound of the plate in real time and adjust the bending parameters to ensure consistent bending effects.
Automation of mold positioning:
High-end equipment has the function of automatic mold positioning and locking, which avoids manual mold loading errors and improves the consistency of mold reuse.
3) Reduce labor costs and labor intensity
Reduce dependence on skilled workers:
Bending work is completed by the system preset program, and ordinary operators only need to do simple monitoring and material handling, which significantly reduces the skill threshold.
Reduce manpower input:
Traditional bending requires 2~3 people to work together, and automated equipment often only requires 1 person to inspect and operate to complete the entire bending production line task.
Reduce labor intensity:
Automatic loading and unloading systems, flexible grippers, etc. reduce direct contact between personnel and heavy objects, avoiding work injuries and muscle strain.
4) Strong flexible production capacity
Quickly switch orders:
The CNC system can save and quickly call multiple workpiece programs to achieve rapid switching from one product to another.
Support multi-specification processing:
Automatic bending equipment can process plates of different thicknesses, sizes and shapes, and adapt to multi-variety, small batch and even customized production needs.
5) Improve the management level and intelligence level of the enterprise
Integrated intelligent manufacturing system:
Automatic bending equipment can be integrated with ERP and MES systems to achieve production scheduling, monitoring, data collection and traceability.
Data-driven optimization:
The system records various processing data, such as processing time, yield rate, energy consumption, etc., to provide a basis for production management optimization.
6) Environmental protection and sustainable advantages
Energy-saving design:
Modern automatic bending equipment mostly uses electric servo drive systems, and energy consumption is reduced by more than 20% compared with traditional hydraulic systems.
Reduce scrap rate:
High-precision processing and program control reduce the number of defective products caused by bending errors and save materials.
Environmentally friendly:
Low operating noise, no hydraulic oil pollution, in line with the concept of green manufacturing.
3. Characteristics of automatic sheet metal bending
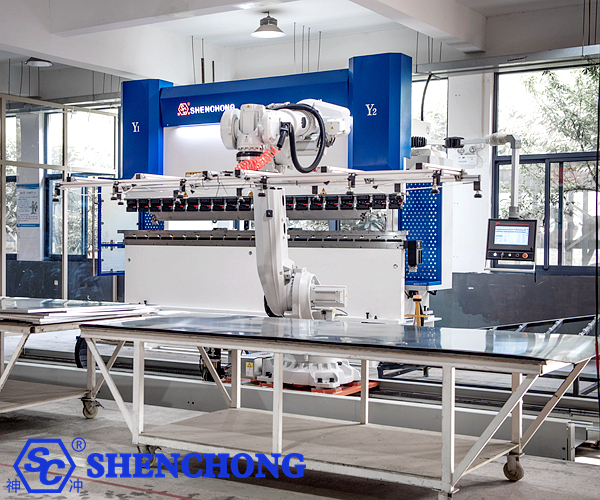
1) High-precision processing
The automatic bending machine is controlled by a numerical control system (such as CNC), and the bending angle and position accuracy can reach ±0.2mm or even higher.
The multi-point compensation system can correct the errors caused by the thickness and material differences of the plate in real time to ensure consistency.
It is particularly important for complex structural parts or high-end products, such as communication equipment, precision electrical cabinets, etc.
2) Significantly improved production efficiency
The bending speed is fast, and the mold change and alignment are fast, which is suitable for high-beat continuous operation.
The automatic bending center can realize the continuous completion of multiple processes, such as multi-angle continuous folding, special-shaped parts forming, etc., greatly reducing the intermediate manual handling time.
With the automatic feeding system and loading and unloading manipulators, unmanned operation is realized, supporting 24-hour continuous production.
3) Good consistency and standardization
All bending actions are controlled by the program, and the size and angle of each product are almost the same, which greatly improves the standardization level of batch products.
It can avoid the “experience bias” in manual operation, improve the final assembly accuracy, and reduce the defect rate.
4) Save labor costs and training costs
An automatic bending center usually only needs one person to supervise or one person to operate multiple machines.
Newbies can operate it with simple training, no longer relying on experienced sheet metal bending technicians, and reducing dependence on technical workers.
5) Strong flexible production capacity
Automatic bending machines support fast program switching and are suitable for small batch and multi-variety production.
It is particularly suitable for customized orders, without frequent mold changes, only program modification.
6) Intelligent integration capabilities
Can access enterprise information systems such as MES and ERP to achieve real-time monitoring of production data, task scheduling, and quality tracking.
Can be integrated with laser cutting, punching machines, and robots to build intelligent sheet metal flexible production lines.
7) Improve product quality and brand image
Higher product consistency and quality are conducive to enterprises entering the high-end market.
Automated production can be used as part of the enterprise’s intelligent manufacturing and Industry 4.0 strategy to enhance market competitiveness.
8) Reduce material waste
Precise bending avoids rework and scrapping, and improves material utilization.
Program control makes it easier to optimize the bending path and reduce mold wear and energy consumption.
If you have a specific scenario, such as what type of sheet metal products (cabinets, sheet metal parts, housings, etc.) you want to process, I can also help you further analyze the appropriate automatic bending line and robotic press brake cell according to your needs.
4. Development trend of sheet metal automated bending
The rapid development of sheet metal automatic bending technology is closely related to the needs of modern manufacturing industry, especially in improving production efficiency, reducing labor costs, and improving bending accuracy.
The development trend of sheet metal automatic bending is showing a multi-dimensional and deep evolution direction with the promotion of concepts such as intelligent manufacturing and Industry 4.0.
The following is a summary of the development trend of sheet metal automatic bending at present and in the next few years:
1) Intelligence and automation
Application of artificial intelligence:
With the development of artificial intelligence technology, sheet metal bending equipment has gradually introduced machine learning and deep learning technologies to achieve more intelligent control. AI can optimize the bending path through data analysis, automatically identify the shape and size of sheet metal, and then adjust the equipment parameters to achieve the best bending effect.
Improved automation:
Modern sheet metal automatic bending machines can already realize a series of automated operations such as automatic loading, automatic bending, and automatic unloading, which greatly reduces manual intervention and improves production efficiency and bending accuracy.
Intelligent detection system:
Through high-precision sensors and visual inspection systems, sheet metal bending machines can monitor and adjust parameters in real time during the production process to ensure the consistency of bending accuracy and quality.
2) Accuracy and flexibility
Improvement of precision control technology:
With the continuous development of CNC technology and servo drive technology, the accuracy of sheet metal automatic bending equipment has been continuously improved, especially when dealing with complex or small-sized sheet metal parts, higher accuracy requirements. High-precision servo motors, precision guide rails and advanced CNC systems have significantly improved the accuracy of the bending process.
Increasing demand for flexible manufacturing:
With the rise of small batch and multi-variety production, companies have higher and higher requirements for the flexibility of sheet metal automatic bending machines. Modern equipment supports rapid switching of bending processes through program control to meet diverse production needs.
Automatic mold replacement technology:
In order to further improve production flexibility, some bending equipment has realized automatic mold replacement. No human intervention is required, which reduces downtime and improves production efficiency.
3) Electrification and green environmental protection
Wide application of electrified drive:
Traditional hydraulic drive is gradually replaced by electrified drive, and the application of electric servo technology makes the drive system of the bending machine more accurate, energy-saving and reliable. The electrified drive system not only improves the bending accuracy, but also reduces energy consumption and maintenance costs.
Green and environmentally friendly manufacturing:
With the improvement of environmental protection requirements, sheet metal automatic bending equipment is gradually developing in a more environmentally friendly and energy-saving direction. For example, energy-saving motors and high-efficiency hydraulic systems are used to reduce energy consumption and pollution emissions.
Reducing waste and optimizing material utilization:
Automatic bending equipment can automatically optimize the material arrangement during the production process through intelligent optimization software, maximize the use of raw materials, reduce waste and reduce costs.
4) Digitalization and Internet of Things (IoT)
Digital production process:
Digital technology enables data tracking, remote monitoring and production scheduling in the production process. Production data can be monitored in real time through the cloud platform to optimize production efficiency and adjust production strategies in time.
Internet of Things and equipment interconnection:
With the development of Internet of Things technology, modern sheet metal bending equipment has begun to have networking functions to realize information sharing between equipment. Through the Internet of Things technology, enterprises can achieve remote management and maintenance of production equipment, improve production efficiency and equipment utilization.
5) Human-machine collaboration and simplified operation
Application of human-machine collaboration:
With the rise of collaborative robots (Cobot), sheet metal automatic bending production lines have gradually realized human-machine collaboration. The combination of collaborative robots and automatic bending machines can not only improve the accuracy of operations, but also greatly improve production efficiency.
Ease of use and intelligent operation:
The operating panel and control system of sheet metal automatic bending equipment are becoming more and more simplified. Many modern equipment are equipped with touch screens and graphical interfaces, allowing operators to set and adjust more conveniently.
6) Efficient material and process innovation
The use of composite materials and new materials:
With the increasing application of new materials (such as lightweight alloys, composite materials, etc.) in industry, sheet metal bending equipment needs to adapt to a wider range of material types. The design and process technology of equipment are gradually developing in the direction of compatibility with multiple materials to improve adaptability.
Bending technology of high-strength steel:
With the widespread application of high-strength steel in automobiles, aviation and other fields, how to bend this material has become a challenge facing the industry. New bending technology needs to overcome the problems of cracks and deformation that may occur in high-strength steel during processing.
7) Digital twin technology
Combination of virtual and reality:
The application of digital twin technology enables sheet metal bending equipment to simulate the actual production process in a virtual environment, so as to predict equipment failures, process bottlenecks, and optimize production processes in advance. This technology can greatly reduce the cost of trial and error and improve production stability.
8) Market demand and industry application
Automobile manufacturing:
In the automotive manufacturing industry, the demand for lightweight and complex-shaped sheet metal parts is increasing, which has prompted bending technology to develop in the direction of high precision and high efficiency.
Home appliances and electronics industry:
The shells of home appliances and electronic products are also usually composed of sheet metal parts, so the demand for automatic bending equipment continues to grow, especially small batch production and customization needs have promoted the development of bending technology.
Aerospace and high-end manufacturing:
High-end manufacturing industries such as aerospace have extremely high requirements for the precision of sheet metal bending, which has prompted related technologies to continue to innovate to adapt to more complex and stringent manufacturing requirements.
The future development of sheet metal automatic bending technology will focus on intelligence, precision improvement, environmental protection and energy saving, and flexible manufacturing. With the continuous development of artificial intelligence, the Internet of Things, digital technology, and new materials, the automation and intelligence level of sheet metal bending equipment will continue to improve, thereby meeting the diversified and high-precision production needs. The sheet metal bending equipment of the future will be more efficient, environmentally friendly, and intelligent, providing better manufacturing solutions for all walks of life.