Table of Contents
Heavy-duty Tandem CNC Press Brake Machines are large-scale CNC sheet metal processing equipment, mainly used for processing super-long, super-thick or special-shaped metal plates. Tandem cnc plate bending machine has become a key equipment for the transformation and upgrading of heavy industrial manufacturing.
It has unique advantages in precision, efficiency, flexibility and automation, and is suitable for the current development trend of Industry 4.0 and intelligent manufacturing. Whether it is processing super-long components, heavy materials, or highly repetitive batch production tasks, it can bring significant production line optimization effects.
1. What is a tandem press brake machine?
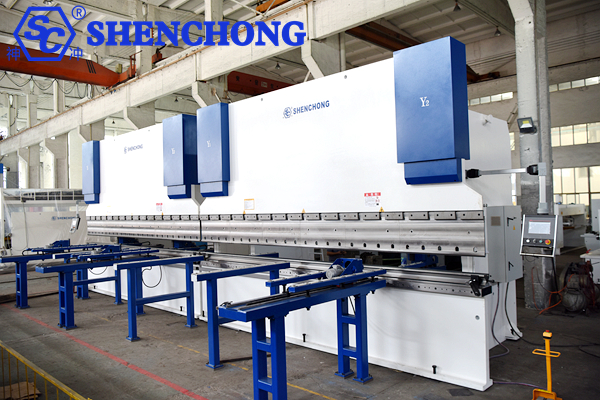
Heavy-duty tandem CNC press brake machines refer to connecting two CNC bending machines through an electronic control system to achieve fully synchronized linkage operation to bend large-format or long workpieces.
Its main features include:
- It can bend longer workpieces (such as 10 meters, 12 meters, or even longer)
- It can process thick plates or high-strength materials
- The two devices can be used independently or in linkage
- High synchronization control accuracy (usually using an electro-hydraulic servo system)
2. Working principle of heavy-duty tandem CNC press brake machines
It consists of two independent sheet metal bending machines working in linkage through the control system to achieve synchronous bending and achieve the purpose of processing large-sized workpieces.
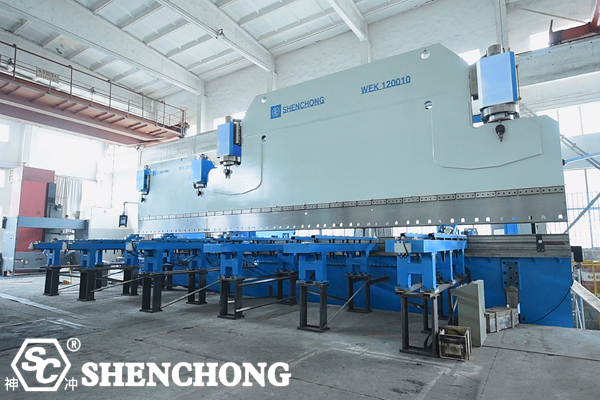
Its basic working principle is as follows:
- Electro-hydraulic servo synchronous control
- Each of the two bending machines is equipped with its own electro-hydraulic servo system and position detection system (such as grating ruler or displacement sensor), and the position of the slider is detected and adjusted in real time through the CNC system.
- The control system will coordinate the synchronous operation of the two sliders to ensure the consistency of the bending angle and position to prevent deviation.
- Synchronous compensation technology
- During the bending process, deformation may occur due to the weight of the workpiece or uneven force on the mold.
- The system will automatically correct the deviation of the slider through the hydraulic compensation device or the mechanical deflection compensation system to ensure the bending accuracy.
- Key auxiliary devices
- Front feedingdevice: support and accurately push large plates.
- Deflection compensation system: automatically correct the mechanical deflection of the slider and the workbench.
- Safety light curtain/laser protection system: ensure the safety of personnel operation.
- Quick mold change device: improve the efficiency of mold change.

- The difference between tandem press brake and an ordinary press brake
Project | Ordinary press brake | Tandem press brake |
Applicable workpiece length | Usually less than 4 meters | Can reach more than 10 meters |
Control method | Single machine control | Dual-machine synchronous control |
Precision control | Single system control | High-precision synchronous control system |
Cost | Low | High |
Application range | Conventional sheet metal processing | Large, extra-long, thick plate processing |
3. Core features of large tandem press brakes
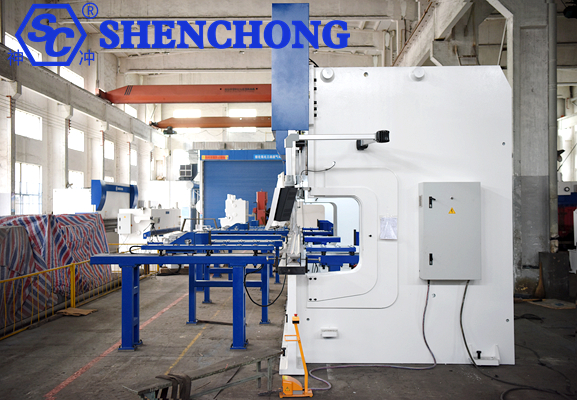
- Super large processing capacity
- The processing length can reach 6 meters, 8 meters, 10 meters, or even more than 12 meters.
- It can process high-strength thick plates, such as 20mm~50mm steel plates, suitable for heavy industries such as shipbuilding, bridges, and wind power.
- Through dual-machine collaborative operation, the capacity of a single machine can be expanded without sacrificing accuracy.
- Dual-machine electro-hydraulic synchronous control technology
- Adopt high-performance electro-hydraulic servo synchronous control system (such as German HAWE or Rexroth).
- The slide action of the two machines maintains high-precision synchronization (error is less than ±0.01mm).
- The position is monitored in real time through a grating ruler or laser detector to ensure bending consistency.
- Intelligent CNC system (CNC) linkage control
- Usually equipped with a dual-channel CNC system (such as Delem DA66T/DA69T or ESA system).
- Support master-slave synchronization, parameter sharing, program linkage, and graphical programming.
- Supports advanced functions such as offline programming, angle compensation, interference simulation, and fault diagnosis.
- Overall deflection compensation device
- Install a hydraulic deflection compensation system to automatically adjust the bending deformation of the slider/worktable.
- Ensure that the bending angles of each section of the super-long workpiece are consistent.
- Some high-end models use an intelligent mold deflection detection feedback compensation system.
- Modular design + can be used independently
- Two bending machines can be used in an online mode or separately.
- Improve flexibility and equipment utilization.
- Save energy and reduce costs for small and medium-sized processing tasks.
- Powerful automation expansion capabilities
- Can integrate forward push devices, support arms, manipulators, and automatic loading and unloading lines.
- Can be docked with robots/AGVs to realize unmanned bending production lines.
- Some systems support MES/ERP system linkage to achieve intelligent manufacturing.
- High-strength structural design
- The frame adopts welding + heat treatment + high-precision processing to ensure long-term stability.
- Key components such as sliders and guide rails are made of imported high-strength steel or composite materials to reduce thermal deformation.
- Multiple safety and auxiliary functions
- Laser safety protection system (DSP, Lazer Safe).
- Photoelectric protection, emergency stop button, anti-collision system.
- Support remote maintenance and diagnosis to reduce downtime.
4. Detailed explanation of the advantages of tandem cnc plate bending machines
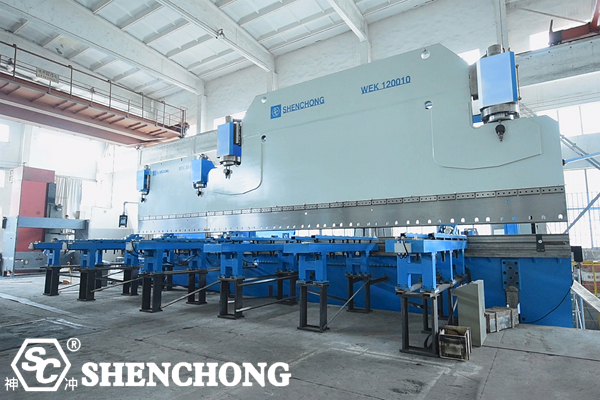
Compared with traditional single-machine press brakes, heavy-duty tandem cnc press brakes have many significant advantages, especially when processing super-long, super-heavy, and complex structural parts, reflecting their unique value. The following are the main advantages of this equipment:
1) Strong ability to process super-long workpieces
- Can handle plates of 6 meters, 8 meters, 10 meters, and even more than 12 meters.
- It is very suitable for large structural parts such as bridges, wind turbine towers, and hull outer plates.
- The length that a single machine cannot cover can be easily achieved through the combination of two machines.
2) Improve bending accuracy
- The two bending machines synchronously control the operation of the slider through the electro-hydraulic servo system.
- Equipped with a high-precision grating ruler/laser measuring device, the error is controlled within ±0.01mm.
- The automatic compensation system can correct the angle deviation caused by the deflection of the long plate.
3) The equipment is highly flexible and can be used independently or in linkage
- The two machines can:
- Link and bend large workpieces.
- Separate and use as two independent bending machines.
- Improve equipment utilization and reduce unit processing costs.
- When the production line is idle, it can handle small and medium-sized order tasks and improve flexible production capacity.
4) Reduce manual labor intensity
- Support configuration of automatic auxiliary devices such as forward push device, plate support arm, and manipulator.
- Particularly suitable for handling heavy workpieces or large parts at high altitudes to reduce handling risks.
- Especially critical for large enterprises (safety + efficiency).
5) High degree of automation and access to intelligent manufacturing systems
- Can be integrated:
- Intelligent mold recognition and rapid replacement system
- Angle feedback system
- CNC graphical programming and remote control interface
- Linked with MES and ERP systems to form a complete chain of Industry 4.0.
- Helps to achieve automated, intelligent, and high-precision mass production.
6) Stable structure and long life
- The fuselage adopts finite element structural analysis design + high-strength welding process + aging treatment, with strong structure and high stability.
- It can maintain accuracy for a long time and is suitable for continuous heavy-load operation.
- Reduce maintenance costs and extend equipment life.
7) Save investment cost (relative to super large single machine)
- Compared with customizing a 12-meter super large single bending machine, using two standard models for linkage:
- Lower cost.
- Easier installation and transportation.
- More flexible maintenance.
5. Analysis of Typical Application Industries of Large-Scale Tandem Press Brake Machines
Heavy-duty tandem cnc press brake machines are widely used in the manufacturing of heavy and extra-long workpieces in many industries due to their high-strength structure, synchronous control system and intelligent integration capabilities. The following is a detailed analysis of their typical application scenarios, advantages and industry value.
1) List of typical applications
Industry fields | Application Description | Functions of bending machines |
Wind power equipment manufacturing | Wind turbine tower, flange joint, cone section | Bending steel plates over 12 meters thick to ensure docking accuracy |
Shipbuilding | Hull outer plate, frame reinforcement plate, deck structure | Processing large curved surfaces and thick plates to reduce welding and trimming |
Bridge structure | Bridge deck steel plate, box beam side plate, support | Bending high-strength steel extra-long plates with precise angle control |
High-voltage power equipment | Transformer shell, switch cabinet frame, large electric box | Processing thick plates and large-size sheet metal shells |
Container and tank manufacturing | Container side plate, tank plate shell, reinforcement rib structure | High-efficiency batch forming of extra-long plates |
Heavy machinery/construction machinery | Crawler chassis, fuselage guard plate, support beam | Bending wear-resistant plates and high-strength structural parts |
Steel structure/steel formwork | Metro/high-speed rail template, structural wall panel, special-shaped plate | High-strength steel, continuous bending at various angles |
2) Analysis of typical application cases
– Wind turbine tower manufacturing
Sheet size: thickness 2040mm, length 812m.
Process requirements: high-strength steel Q355, Q420, after forming, it needs to be precisely butted and welded with the cylinder.
Bending requirements: bending accuracy within ±0.5°, high deflection compensation requirements.
Advantages of bending machines:
High tonnage (such as 2×600 tons) linkage operation.
Intelligent compensation for slider deflection.
Support automatic feeding and angle feedback correction.
– Bridge steel structure processing
Sheet types: H-shaped steel wing plate, box girder side plate.
Process challenges: long bending length and structural center of gravity offset.
Advantages of bending machines:
Can push the material forward to avoid the “whip tail effect” of the sheet.
Laser positioning + CNC graphic control ensures symmetry.
– Container mass production
Process characteristics: long and thin workpieces, large batches, and frequent changes.
Advantages of bending machines:
Rapid mold change system.
Cooperate with automatic loading and unloading device/AGV to form an automatic line.
Multiple bending at one time improves production efficiency.
3) Application value and benefit improvement
- Productivity improvement: Dual-machine linkage can process larger plates, reduce workpiece splicing, and improve efficiency by 30~50%.
- Machining accuracy improvement: Synchronous control + automatic compensation + CNC positioning, significantly reducing bending errors.
- Labor optimization: Reduce dependence on highly skilled operators, achieve less manpower and automation.
- Improved quality stability: Large workpieces can achieve “one-time bending and forming”, reducing welding finishing and deformation.
- High return on equipment investment: It can take into account both large and small tasks, improve equipment utilization and return on investment.
- Intelligent manufacturing integration: It can be connected with MES/ERP systems to achieve real-time production monitoring and management analysis.
6. Summary
Heavy-duty tandem cnc press brake machines is a high-end equipment used for bending processing of super-long, super-thick and super-heavy plates, which is controlled and operated synchronously by two CNC metal sheet bending machines (usually electro-hydraulic servo synchronous bending machines) of the same specifications through the CNC system. It is widely used in heavy industries such as wind power, bridges, ships, steel structures, power equipment, etc., and is an important part of modern intelligent sheet metal processing.
Features Analysis Table:
Feature classification | Advantages |
Processing range | Extra-long and extra-thick plates, suitable for large components |
Precision control | High-precision electro-hydraulic synchronization + deflection compensation |
System control | Intelligent CNC control, supporting master-slave linkage |
Automation expansion | Supporting robots, front pushers, AGV and other intelligent accessories |
Application flexibility | Modular combination, can be used alone |
Safety and maintenance | Multiple protection + remote diagnosis capabilities |
Advantages Analysis Table:
Category | Advantages |
Processing capability | Processing of extra-long and extra-thick workpieces, breaking through the limitations of a single machine |
Control accuracy | Electro-hydraulic synchronization + CNC control, high precision, strong compensation |
Flexibility | Can be linked/separated to adapt to a variety of production needs |
Automation | Supports manipulators and feeding devices to reduce manual dependence |
Economy | Moderate investment, strong versatility, easy maintenance |
Intelligence | Can be connected to the intelligent manufacturing platform to realize a digital factory |
Typical application scenarios table:
Application industries | Typical products |
Wind power industry | Tower plates, flange reinforcement plates, barrel cone plates |
Bridge steel structure | Box beam side plates, support plates, truss structures |
Shipbuilding | Hull outer plates, deck hatches, bulkheads |
Electric power equipment | Large transformer housings, high-voltage cabinet structures |
Construction machinery | Heavy crawler housings, boom frames, support plates |
Steel structure building | Large curtain walls, steel formwork, prefabricated components |
Heavy-duty tandem press brake is not only a powerful tool to solve the problem of bending super-long and heavy plates, but also an important equipment for enterprises to move towards high-end manufacturing and intelligent production lines. It is superior to traditional bending methods in terms of precision, efficiency, flexibility, safety and intelligence, and is becoming the mainstream solution for heavy industry and large-scale sheet metal processing.
If you are selecting a model for a specific project, please provide your required parameters (plate thickness, length, daily processing volume, etc.), and we can recommend a detailed technical solution for you.