Table of Contents
The automated bending development trend of metal sheets is rapidly developing towards high precision, high efficiency, flexibility and intelligence, driven by the digitalization and intelligent transformation of the manufacturing industry.
As an important part of the intelligent upgrading of sheet metal processing, sheet metal automated bending has developed rapidly in recent years. The following is an analysis of the development trend of automated bending, mainly from the perspectives of technological progress, industrial application, and intelligent manufacturing integration.
1. Background and current status of automated bending
Metal sheet bending is one of the key processes in sheet metal manufacturing. Traditional bending methods rely on manual operation, which has problems such as low efficiency, unstable precision, and high labor intensity. With the advancement of laser cutting, robots, and intelligent control technologies, automated bending has gradually become the mainstream.
2. Analysis of sheet metal automated bending development trend
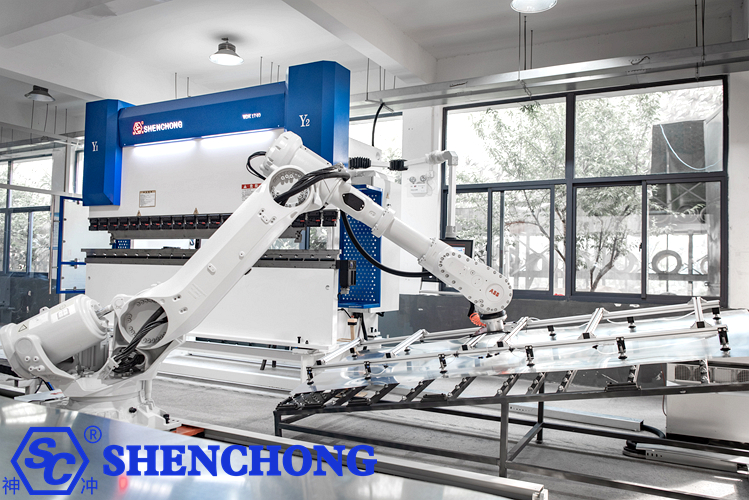
The future trend of automated bending of metal sheets is an important part of building an “unmanned, intelligent, and flexible” production system. It will help sheet metal processing companies achieve the transformation from “manufacturing” to “intelligent manufacturing”, improve efficiency, reduce dependence on manpower, and ensure product quality, thereby occupying a favorable position in the fierce market competition.
1) Intelligent equipment upgrade
- Popularization of CNC technology: Bending machines are generally equipped with CNC numerical control systems to achieve precise control of angles, positions, and pressures.
- AI+ bending applications: Introduce AI algorithms to automatically optimize bending sequences, springback compensation, interference prediction, etc.
- Visual recognition system integration: Improve positioning accuracy and quality inspection levels, and support automatic centering and angle measurement of plates.
2) Automated collaborative system integration
- Robot collaborative bending: Use industrial robots to complete loading and unloading, flipping, bending and other processes to achieve unmanned operation.
- Front and rear feeding system matching: Cooperate with front feeding trusses, rear discharge sorting and other systems to improve the overall production line automation efficiency.
- Flexible fixture and suction cup technology: Adapt to the automatic handling and positioning of plates of various sizes and shapes.
3) Flexible manufacturing of small batches of multiple varieties
- Flexible production unit construction:
With functions such as fast mold change and tool change, it can meet the switching needs of multiple varieties.
- Intelligent scheduling and automatic program generation:
Combine MES system with CAD/CAM system to realize automatic generation and scheduling of bending programs.
- Application of digital twin technology:
Simulate bending paths and processes in advance to avoid interference and errors, and improve the success rate of the first piece.
4) Continuous improvement of precision and quality
- Real-time angle detection and compensation: use angle sensors and laser measurement to achieve closed-loop control to ensure angle consistency.
- Automatic mold identification and centering: the system can identify mold models and positions to avoid incorrect clamping and improve efficiency.
- Material property identification: the system can automatically adjust the bending force according to material thickness and type to optimize quality.
5) Green manufacturing and energy saving and environmental protection
- Promotion of servo electric bending machines: replace traditional hydraulic structures, save energy and reduce noise, and reduce environmental problems such as oil leakage.
- Application of hybrid power systems: oil-electric hybrid models take into account both power and energy efficiency, and are suitable for medium and large bending equipment.
- Energy consumption monitoring and management system: realize statistical analysis of electricity and oil consumption data, and support energy-saving and cost-reduction decisions.
3. Typical application industries
With the promotion of strategies such as intelligent manufacturing, Industry 4.0 and Manufacturing 2025, traditional manual bending methods are difficult to meet the needs of high efficiency, high precision and small batch multi-variety production. Automated bending technology has emerged.
- Sheet metal processing workshop: small and medium batch multi-variety production scenarios, automated transformation to improve production capacity.
- Home appliance manufacturing: pursuit of appearance consistency and high precision requirements, automatic bending effect is more stable.
- Auto parts: high degree of standardization, suitable for robot integrated operation.
- Electric cabinets and electrical boxes: need to be folded multiple times and multiple sides completed at one time, bending center system is widely used.
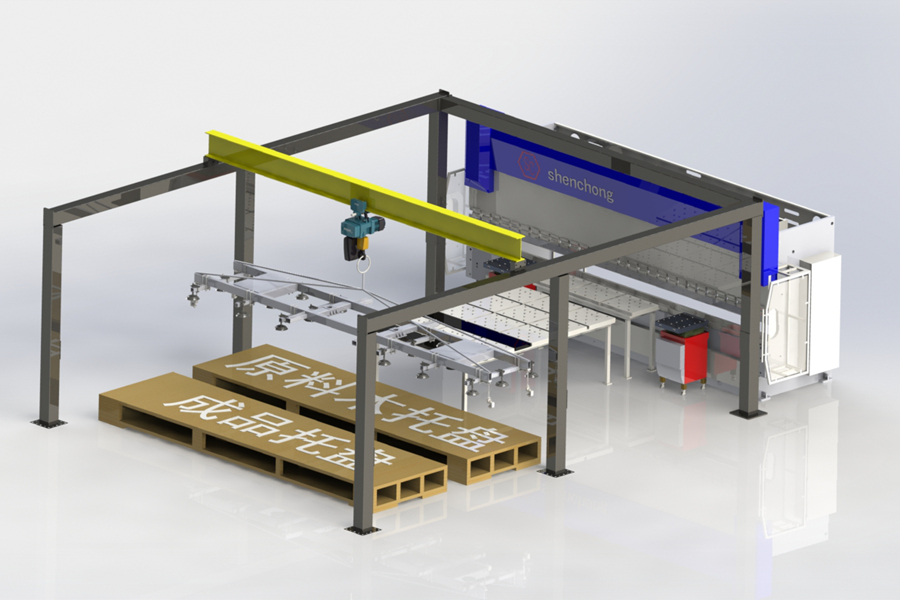
4. Typical representative technologies and equipment
- Hybrid servo CNC press brake machine: such as AMADA, TRUMPF, SHENCHONG and other corporate products.
- Robot automatic bending unit: ABB, STEP, KAWASAKI jointly provide customized solutions with sheet metal automation integrators.
- Intelligent bending center (panel bender): supports full-process automatic bending, including loading and unloading, flipping, detection, classification, etc.
5. Future development prospects of automated bending of metal sheets
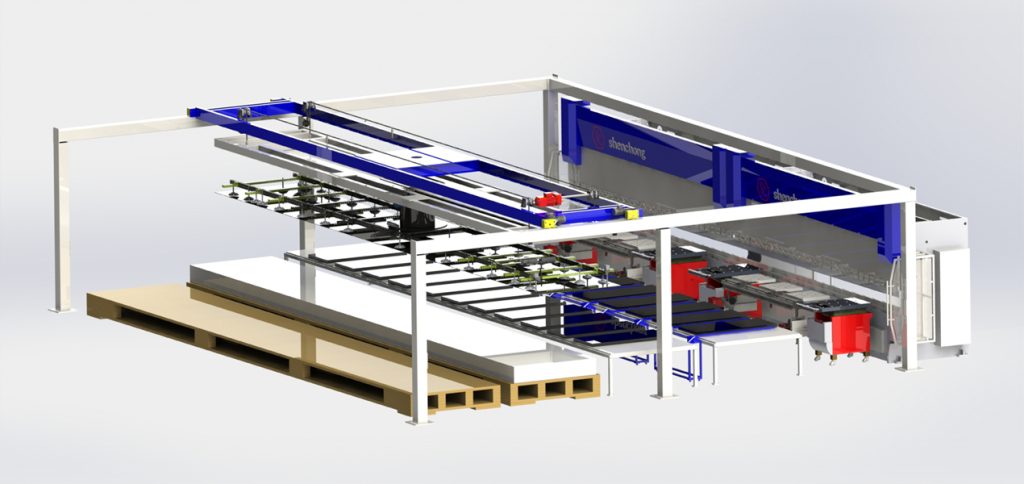
The future development prospects of automated bending of metal sheets are very broad, and its core driving force comes from the continuous advancement of intelligent manufacturing, rising labor costs, and the continuous pursuit of high-precision and high-efficiency production.
1) Broad prospects for industrial development
With the continuous growth of demand in industries such as automobiles, new energy, sheet metal manufacturing, home appliances, elevators, and electrical control cabinets, the demand for automated, efficient, and precise bending is becoming more and more urgent. Automated bending technology will continue to expand in the following directions:
Market demand is growing steadily:
The trend of customization and batch diversification is accelerating, promoting the development of flexible bending systems.
With the upgrading demand of “machine replacement”, small and medium-sized factories have also begun to gradually introduce automated bending equipment.
Export-oriented enterprises and international brands have higher quality requirements, promoting high-end equipment.
2) Continuous evolution of core technologies
- Servo and electrification upgrades
Servo electric bending machines will gradually replace traditional hydraulic models, with higher energy efficiency, stability and precision.
Reduced energy consumption and maintenance costs promote green manufacturing.
- AI and big data integration
AI intelligent bending system can automatically identify the type and thickness of the plate and generate processing solutions.
Data-driven predictive maintenance improves equipment utilization and reduces downtime.
- Popularization of digital twin technology
Real-time simulation of the bending process, verification of processing feasibility, avoidance of interference, and improvement of the first-piece success rate.
Provide support for remote debugging and visual production.
3) Enhanced integration capabilities of the bending system
- Highly integrated automated production lines
Automatic bending systems will be seamlessly connected with laser cutting, stamping, welding, grinding, packaging and other systems.
Realize the “integrated intelligent manufacturing unit” of sheet metal and improve overall production capacity and response speed.
- Comprehensive popularization of robot collaboration
Industrial robot bending, loading and unloading, flipping and positioning have become a trend.
The human-machine collaboration system ensures safety while improving efficiency, and adapts to small batches and variable tasks.
4) Intelligent manufacturing platform support
MES, ERP, WMS and other systems will be deeply integrated with bending process data.
Cloud platform remote diagnosis, energy efficiency management, and fault warning systems are becoming increasingly mature.
The “edge control + cloud decision-making” model improves response speed and intelligence level.
5) Forecast of automated bending key future development directions
Development direction | Content Overview |
Flexible production | Quick mold and material change system to achieve fast switching of multiple varieties |
Intelligent adaptive control | Real-time adjustment of bending force and angle to adapt to the differences of different materials |
Full process unmanned | Fully automatic completion from feeding → bending → detection → discharging |
Cloud collaborative manufacturing | Bending data sharing and scheduling optimization between factories to improve resource utilization |
Service-oriented manufacturing model | Transform from “selling equipment” to “selling capabilities” to provide overall bending solutions |
6. Summary: Automated bending is a key node of "intelligent manufacturing upgrade"
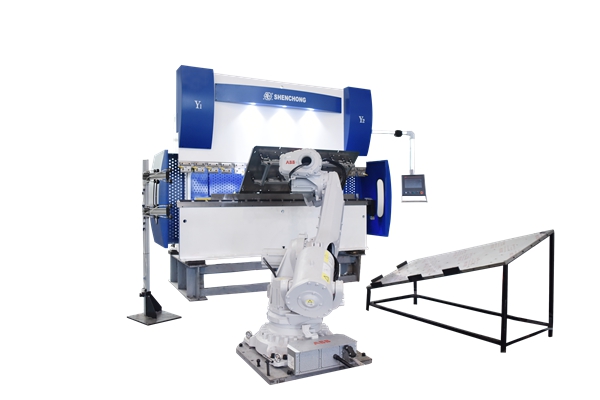
Automated bending of metal sheets will gradually enter a new stage of “high intelligence, high flexibility, low energy consumption, and full coordination”, which will not only improve production efficiency and product quality, but also help enterprises build digital, intelligent, and green core competitiveness. It has great potential for future development, especially in the following scenarios:
- High-end manufacturing (such as aviation, new energy)
- Flexible customization (such as sheet metal customized home)
- Smart factory construction
- “Industry 4.0” and “Smart Manufacturing 2025” implementation