Table of Contents
Laser cutting machines are widely used in industrial manufacturing, but due to their high energy and high precision, they are also accompanied by certain safety risks. The following is a comprehensive analysis of laser cutting machine safety issues, including potential risks, safety protection measures, usage specifications and emergency response.
1. Main safety risks of laser cutting machines
Laser radiation injury
The laser emitted by laser cutting machines is usually a high-power laser (such as CO₂ laser or fiber laser). If it is not properly protected, it will cause irreversible damage to the eyes and skin.
Fire risk
The high temperature of laser cutting can easily ignite flammable materials, or sparks generated during the cutting process can cause fires.
High temperature burns
The cutting area is extremely hot, and contact with the material or nozzle can easily cause burns.
Smoke and harmful gases
Cutting certain materials (such as PVC, plastic, composite board, etc.) will release toxic gases that are harmful to the respiratory system.
Electrical hazards
The high-voltage system and control system of laser equipment have the risk of electric shock.
Mechanical injuries
If the running parts of the equipment (such as motors and tracks) are not safely protected, there is a risk of pinching and collision.
2. Laser cutting machine common safety issues
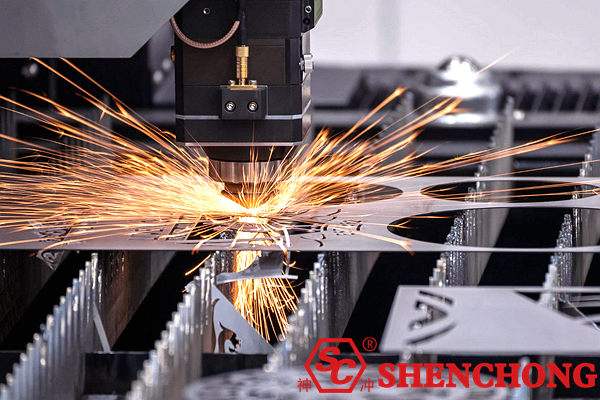
Common safety issues of laser cutting machines:
Safety issue types | Specific problem performance | Potential harm |
Laser radiation | Failure to wear goggles, laser beam scattering, light path exposure | Eye injuries, skin burns, blindness |
Fire risk | Cutting flammable materials, sparks flying, no fire extinguishing device | Material fires, equipment damage, personal injuries |
Toxic smoke and gas | Cutting plastic, leather, PVC and other materials releases poisonous gases | poisoning, respiratory disease |
High temperature burns | Burns caused by touching hot workpiece or nozzle, or material falling | Skin burns, accidental downtime |
Electrical risk | Equipment wiring is loose, leakage, or private power supply | Electric shock, fatal shock |
Mechanical injury | Hands enter the movement range of the cutting head and parts suddenly move | Bump, pinch, fracture |
Operational error | Parameter setting errors and equipment misoperation | Scrapped materials, equipment damage, accidents |
Corresponding solutions to safety issues:
Problem categories | Safety solutions |
Laser radiation | Use a closed cutting chamber |
Fire risk | Wear goggles that match the laser wavelength |
Toxic smoke and gas | Set up warning signs in the laser area and no unauthorized entry |
High temperature burns | Avoid cutting flammable materials (such as foam, cardboard, etc.) |
Electrical risk | Equip with dry powder fire extinguishers |
Mechanical injury | Set up smoke and temperature alarm systems |
Operational error | Install high-efficiency ventilation systems or smoke purifiers |
3. Laser cutting machine safety protection measures
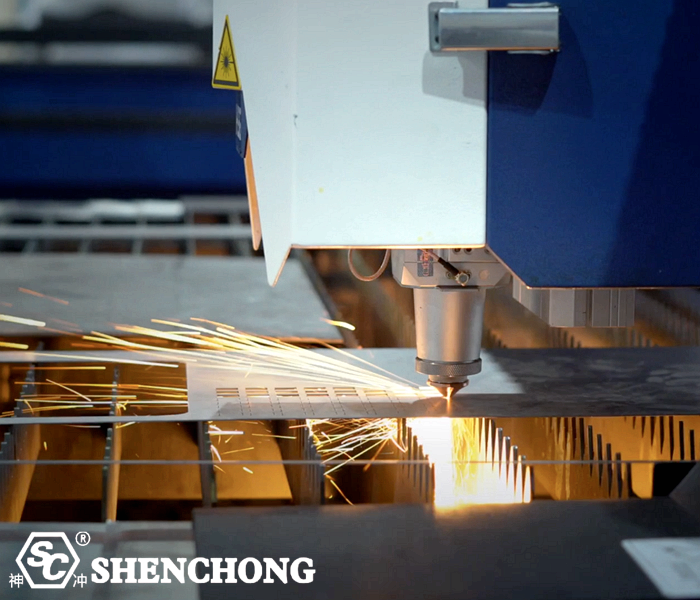
Wear protective glasses and protective clothing
Use professional protective glasses corresponding to the laser wavelength and wear fire-resistant clothing to prevent burns or injuries.
Use closed or partially closed laser cutting machines
Prevent laser radiation exposure to operators to the maximum extent.
Install exhaust systems and filters
Effectively remove smoke and harmful gases generated during cutting to keep the air clean.
Set up fire alarm and fire extinguishing devices
Especially when cutting combustible materials, smoke alarms and automatic fire extinguishing systems are required.
Electrical safety management
The equipment should be maintained by certified electricians, the wires should be well grounded, and leakage protection devices should be installed.
Mechanical protective devices are intact
Install emergency stop buttons, protective covers, limit switches, etc. to prevent mechanical injuries caused by misoperation.
4. Laser cutting operation and use specifications
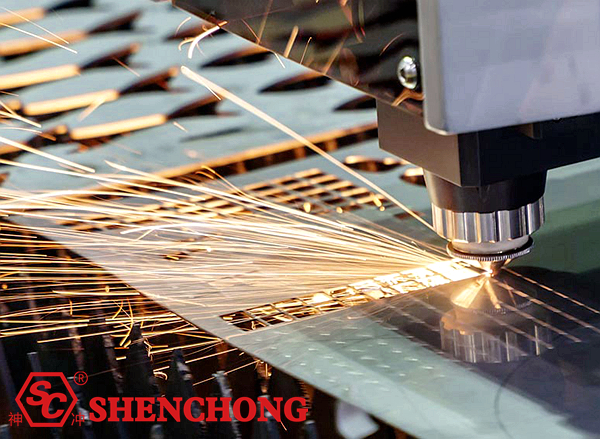
Pre-job training
All operators must undergo professional training and assessment and be familiar with the equipment structure and operation procedures.
Pre-operation inspection
Confirm that the equipment is intact, the power supply is grounded, the cooling system is normal, and the laser parameters are set correctly.
It is strictly forbidden to operate the laser without load
Laser emission should only be carried out when the material is in the cutting position to avoid damage caused by empty hitting.
It is not allowed to dismantle the equipment or modify the program without authorization
Unauthorized personnel are not allowed to dismantle or repair the equipment or change the control parameters.
The principle of dedicated care
No one should be left alone during the laser cutting process to prevent abnormal situations from not being handled in time.
5. Laser cutting machine safety operation guide
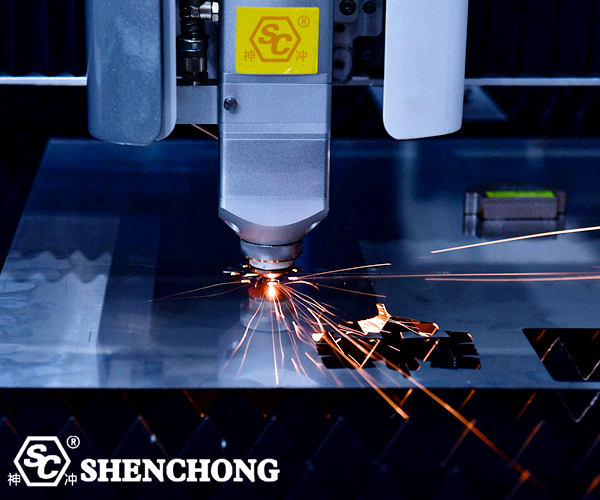
1) Preparation work before operation
Equipment inspection
- Optical path inspection: Confirm that the laser optical path system is not damaged, and the optical mirror, reflector, and focusing lens are not cracked or dirty.
- Power supply inspection: Check the electrical system to ensure that the cable is firmly connected, not exposed, and has leakage, and ensure that the grounding is good.
- Gas inspection: Confirm whether the pressure and flow of the gas system (such as oxygen, nitrogen, and air) are normal, and the storage position of the gas cylinder meets laser cutting safety requirements.
- Cooling system: Check the coolant volume and whether the cooling system is operating normally.
Personnel protection
- Goggles: Wear protective glasses suitable for the laser wavelength to prevent laser radiation from damaging the eyes.
- Protective clothing: Wear fire-proof and anti-electromagnetic radiation protective clothing to avoid being injured by high-temperature gas or sparks during the cutting process.
- Gloves and earplugs: Wear heat-insulating gloves and necessary earplugs to prevent mechanical damage and noise hazards.
Working environment inspection
- Workbench stability: Ensure that the cutting table or workpiece support is stable and does not shake, and ensure that the cutting piece is fixed.
- Clean and free of debris: The work area should be kept clean and away from flammable items (such as oilcloth, paper, plastic, etc.).
- Good ventilation: Ensure that the ventilation equipment is working properly to avoid the accumulation of toxic gases and smoke.
2) Precautions during operation
Equipment startup
- Startup sequence: Start the equipment according to the equipment manual or operating procedures, start the cooling system first, then start the laser and control system.
- Laser mode setting: Ensure that the parameters such as laser power, cutting speed and auxiliary gas pressure are set correctly.
- Check the cutting path: Before starting the laser, check the accuracy and clarity of the cutting path to ensure that there are no interferences.
Notes during cutting
- Material fixation: Ensure that the workpiece is firmly fixed during the cutting process to avoid cutting errors or sparks due to vibration or sliding during the cutting process.
- Observe the cutting status: The operator needs to observe the cutting status at any time, especially abnormal phenomena such as sparks, odors, and smoke. Once a problem is found, stop the operation immediately.
- Do not leave the work station: The operator should remain at the post during the cutting process. It is strictly forbidden to leave without authorization to prevent the operator from being unable to respond in time when an emergency occurs.
Emergency stop and emergency treatment
- Emergency stop button: There must be an obvious emergency stop button on the equipment. If you encounter any danger or abnormal situation, press the emergency stop button immediately.
- Fire handling: During the cutting process, if a fire or overheating occurs, use fire extinguishers, fire extinguishers and other equipment to extinguish the fire in time. Never use water to extinguish electrical fires.
- Gas leakage handling: If a gas leak is found, the gas cylinder valve should be closed immediately and the relevant personnel should be notified for handling.
3) Cleaning and maintenance after operation
Equipment shutdown
- Correct shutdown sequence: According to the sequence of the equipment operation manual, turn off the cooling system, laser and main power supply to ensure that the equipment is completely powered off.
- Cleaning equipment: After shutting down, use a soft cloth to clean the laser head, workbench and surrounding environment. Clean cutting waste, lens, optical path and airflow duct regularly.
Equipment maintenance
- Regular inspection: Regularly check the laser lens, reflector, workbench, cooling system, etc. to ensure that the equipment is running well.
- Replacement of wear parts: According to the usage, timely replace damaged or aging parts such as laser lenses and sealing rings.
- Record maintenance log: Fill in the equipment maintenance log after each maintenance to track the equipment usage status.
6. Suggestions on safety management of laser cutting machines
System construction:
- Formulate laser equipment operation specifications, inspection system, and accident reporting system
- Organize laser cutting machine safety training and emergency drills regularly
- Appoint a dedicated person to be responsible for safety inspection and rectification tracking
- Equipment maintenance:
- Regularly replace laser lenses, check the position of laser heads and cooling systems
- Clean the exhaust system to prevent carbon deposits from causing fires
Employee management:
- Implement “certificate-based employment” and no operation is allowed without training
- Establish an operation responsibility system and implement safety responsibility traceability
The key to laser cutting safety management lies in:
Equipment safety + operation specifications + environmental protection + adequate training
Strengthening on-site inspections, hidden danger inspections, and emergency drills is a guarantee for preventing problems before they occur.
7. Emergency Response Plan
Risk types | Emergency measures |
Laser injury | Stop the equipment immediately, rinse the injured part with plenty of water and seek medical attention |
Burns | Rinse with cold water for at least 10 minutes to avoid skin damage, and seek medical attention immediately |
Fire | Disconnect the power supply immediately, use a dry powder fire extinguisher to put out the fire, and call the police and evacuate if the fire cannot be controlled |
Poisoning (inhalation of harmful gases) | Move to a ventilated place quickly, and seek medical attention immediately if symptoms occur |
Electric shock | Disconnect the power supply, use insulating tools to rescue, do not directly touch the injured, and perform cardiopulmonary resuscitation when necessary |
8. Summary
Laser cutting machines are widely used in manufacturing, sheet metal, advertising and other industries. In order to ensure the personal safety of operators and the stable operation of equipment, it is necessary to fully understand and prevent the possible safety risks. The above is a guide to safe operation of laser cutting machines, which aims to help operators understand and follow safety regulations to ensure safe and efficient use of laser cutting machines.
The operation of laser cutting machines involves multiple links, and safe operation is the basis for ensuring efficient production and personal safety. Through strict operating procedures, regular safety inspections and equipment maintenance, we can effectively reduce the risk of accidents and ensure the safety of the production environment.