Table of Contents
Electrical servo CNC panel benders are advanced equipment that uses an electric servo system as the core power source and is precisely controlled by a CNC program for automated folding of sheet metal workpieces. The maintenance of the electrical servo CNC panel benders is extremely important, which not only affects the operating efficiency, processing accuracy and service life of the equipment, but also directly affects the production safety, cost control and delivery capabilities of the enterprise.
1. Basic composition of electrical servo CNC panel benders
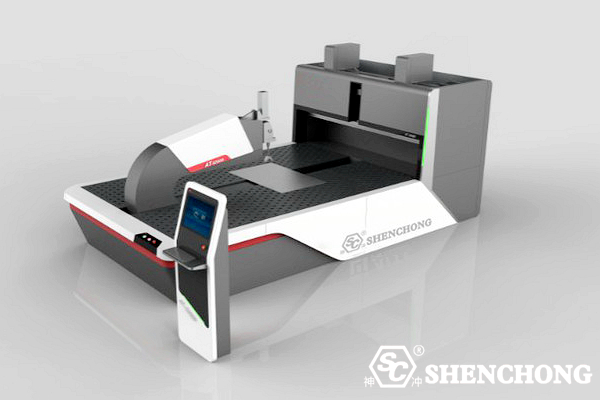
The electrical cnc panel bender is an intelligent device specially used for multi-station, high-precision sheet metal processing such as flanging, folding, and forming of metal sheets. It is particularly suitable for the automated processing of complex bending processes such as 90°, reverse bending, Z folding, and curve folding on the product edge. It is an upgraded device for more complex sheet metal edge forming needs after the CNC bending machine. It is also commonly called:
- Flexible bending center
- Servo bending unit
- Intelligent panel bender workstation
Equipment structure table:
Module | Functional description |
Servo motor system | Provide power to drive the movement of each axis, replacing the traditional hydraulic system, with fast response, high precision and low energy consumption |
Folding system | The folding knife moves forward and backward to complete bending at different angles, including positive folding, reverse folding, double folding, Z-shaped folding, etc. |
Pressing system | Use servo-controlled clamps to clamp the plate stably to ensure that it does not move during processing |
CNC control system | CNC interface programming and control, which can integrate automatic compensation, 3D simulation, fault diagnosis and other functions |
Automatic feeding system (optional) | With a robotic arm or suction cup device, it can realize automatic loading and unloading and multi-station handling |
The difference between the automatic electrical servo CNC panel bender and the traditional plate bending machine:
Comparison dimensions | Automatic panel bender | Traditional flanging machine |
Mold dependence | Few or even no molds | Requires a large number of customized molds |
Product switching | Quick switching, no need for long downtime | Time-consuming mold change, difficult to cope with multi-variety production |
Control method | CNC+servo drive+parametric programming | Mechanical adjustment, poor repeatability |
Degree of automation | High, can integrate robots and intelligent production lines | Low, usually manual loading and unloading |
2. Core advantages
Electrical servo CNC panel benders are CNC device that is driven by a servo motor and controlled by a CNC system to automatically flanging sheet metal workpieces through multi-axis linkage. It is widely used in edge forming of sheet metal shells, chassis cabinets, electrical panels, automotive parts, etc.
Compared with traditional hydraulic bending equipment, it has comprehensive advantages in precision, efficiency, environmental protection and intelligence, and is one of the important equipment of intelligent sheet metal factories.
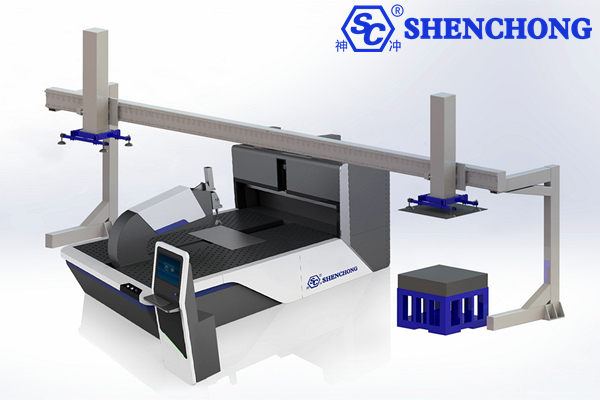
Advantages list of electrical servo CNC panel benders:
Advantages | Detailed description |
High bending accuracy | Servo motor closed-loop control, repeatable positioning accuracy can reach ±0.05°, and the bending consistency is extremely high |
Quick changeover | No need to change molds frequently, support program switching, automatic adjustment of paths and angles, suitable for small batches of multiple varieties |
Energy saving and environmental protection | Compared with hydraulic presses, energy consumption is reduced by 30~50%, no hydraulic oil leakage, and low operating noise |
High degree of intelligence | Integrated MES/ERP, 3D graphics simulation, bending database, remote diagnosis and pre-maintenance reminder functions |
Safe and reliable operation | Equipped with grating protection, emergency stop system, and safety door interlocking mechanism to ensure operator safety |
Strong scalability | Support supporting robots, AGV logistics, code scanning recognition, etc. to realize intelligent sheet metal production lines |
Functional features of cnc panel bending centers:
Features | Description |
High flexibility | Can adapt to various workpiece shapes without changing the mold |
Multi-station combination processing | Panel bender + forming + trimming are completed in one go, reducing the transfer process |
Excellent precision control | Electric servo control, angle error within ±0.1° |
Automatic program scheduling | Supports importing CAD drawings to generate flanging paths |
Intelligent detection and compensation function | The system can automatically identify plate thickness differences, material rebound and adjust parameters |
Typical application industries:
- Chassis and cabinet manufacturing (such as power and communication cabinets)
- Sheet metal home appliance housing (such as air conditioners and refrigerator panels)
- Elevator door panels, elevator sheet metal structural parts
- New energy vehicle battery shells, pallet folding parts
- Stainless steel kitchen equipment, medical equipment structural parts
Applicable industries and typical workpieces list
Industry fields | Application examples |
Electrical sheet metal | Chassis panels, electric meter boxes, air conditioning ducts, washing machine back panels |
Cabinet and casing | Power cabinets, communication cabinets, server housings |
Automobile manufacturing | Battery pack housings, body structure reinforcements |
Kitchen and bathroom equipment | Hood covers, stainless steel sinks, operating tables |
Medical/environmental protection equipment | Stainless steel housings, medical racks, purification system panels, etc. |
3. The importance of maintenance of electric servo CNC panel bending machines
The maintenance of electric servo CNC panel benders is crucial. It is not only related to the operating efficiency, processing accuracy and service life of the equipment, but also directly affects the production safety, cost control and delivery capabilities of the enterprise. The following is a specific analysis of the importance of its maintenance.
1) Ensure high-precision and stable operation of the equipment
The electric servo CNC panel benders rely on a high-precision servo control system. If problems such as improper lubrication, zero drift, and guide rail wear are not handled in time, it will lead to:
- Increased folding angle error
- Workpiece deformation and reduced yield rate
- CNC program execution accuracy is affected
Regular maintenance can prevent processing accuracy drift and maintain a repeatability accuracy of ±0.1°.
2) Extend the service life of the equipment and avoid high maintenance costs
Key components such as servo motors, ball screws, and guide rails are expensive, such as:
- Motor overload and failure to clean will cause burning
- Lack of lubrication on the slide rail may cause irreversible wear.
Daily cleaning and lubrication can extend the service life of the equipment by more than 3 to 5 years.
3) Reduce the risk of sudden downtime and ensure production continuity
Sheet metal production usually has high requirements for delivery cycle. Once the equipment stops due to failure, the consequences include:
- The whole line stops production
- Cumulative order delays
- Damage to brand reputation
Regular inspections and preventive maintenance can reduce more than 80% of unplanned downtime.
4) Improve operational safety and prevent human-machine accidents
CNC panel bending machines are high-power equipment. If safety functions such as safety photoelectric, emergency stop buttons, and limit sensors fail due to lack of testing, it will seriously threaten personnel safety.
Regular safety system self-inspection and functional testing are key means to ensure employee safety.
5) Maintain energy efficiency and save energy and reduce consumption
If the servo system accumulates dust and poor cooling for a long time, it will lead to:
- Increased power consumption
- System load temperature rises and efficiency decreases
Cleaning the heat dissipation channel and fan filter can ensure energy-saving operation of the system and reduce electricity expenses.
6) Improve intelligent management and data traceability capabilities
With the development of equipment networking, maintenance records have become an important data support in MES and equipment management systems (EMS):
- Provide a basis for fault diagnosis
- Optimize maintenance plans
- Assist in production decision-making
Establishing standardized maintenance files will help enterprises achieve digital management of equipment.
4. How to maintain CNC electric servo panel bender machine?
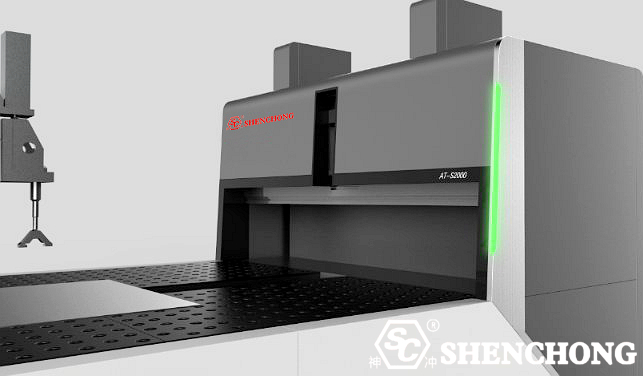
1) Daily inspection and maintenance (before starting the machine every day)
Item | Contents |
Power System | Check whether the power wiring is loose or ablated. Confirm that the voltage is normal (±10%). |
Servo Drive Unit | Check whether there is an alarm indication. Check whether the fan is cooling smoothly. |
Clip system | Check whether the clamping claws/suction cups are clean, without jamming or damage. |
Folding knife components | Check whether the folding knife has cracks, wear, jamming and other abnormalities. |
Clean | Wipe the outside of the equipment to prevent metal dust accumulation. |
2) Weekly maintenance item sheet
Items | Method or standard description |
Slide rail/guide rail lubrication | Use the manufacturer’s specified grease (such as lithium-based grease), clean and relubricate |
Fixing bolt inspection | Check whether the main transmission structure, tool holder, bearings and other key parts are loose |
Cable hose inspection | Check whether the cable drag chain and cable sleeve are worn, cracked, or detached |
Operation panel button test | Confirm that the emergency stop, start, reset and other buttons function normally |
3) Monthly maintenance items table
Item | Content Description |
CNC System Backup | Back up the program and parameters to a USB/U disk or network server |
Servo System Diagnosis | Read the servo drive alarm record, current, temperature and other indicators during operation to determine whether there is an abnormality |
Check the gear/timing belt | Check whether the transmission device is loose, broken, or worn |
Clean your cooling system | Clean the control cabinet fan filter and servo drive heat sink to prevent overheating |
4) Quarterly/half-year maintenance items
Item | Content |
software upgrades | Check whether the CNC system has an official upgrade package to improve stability and new functions |
position calibration | Recalibrate the zero point of the XYZ axis or the main folding axis to maintain accuracy |
Check safety system | Check whether the photoelectric protection, door lock, and emergency stop circuit functions are effective |
Insulation and ground detection | Use a megohmmeter to check whether the ground insulation resistance value of the motor and driver is qualified |
5) Annual inspection recommendations (recommended to be performed by the manufacturer or professional service provider)
Item | Description |
Complete machine accuracy testing | Test and adjust the accuracy of repeated bending angles, tool centerlines, etc. |
Comprehensive inspection of the electronic control system | Check whether the PLC, CNC controller, servo drive, and relays are aging or have hidden dangers |
Servo motor status evaluation | Check whether there are abnormal temperature rise, abnormal torque, encoder drift, etc. |
Machinery wear analysis | Measure the wear of key parts such as screws, ball guides, and bearings and provide replacement suggestions |
6) Common faults and solutions
Fault phenomenon | Possible cause | Suggestions |
Servo alarm (overload, overtemperature) | Motor stuck, overloaded, poor ventilation | Stop the machine to check the load/fan/cleaning status |
Large folding angle error | Zero offset, workpiece slippage, insufficient clamping | Re-calibrate, check the clamping force and process parameters |
Unable to start/run | Safety door is not closed and emergency stop is not reset. | Check all safety switches and release the emergency stop button |
CNC unresponsive or frozen | Program errors, abnormal voltage | Restart the system or restore to factory settings |
7) Maintenance material recommendation table
Material name | Recommended models/specifications |
Grease | Japan THK lithium-based grease/AW-32 gear oil, etc. |
Fan filter | General specifications can be purchased according to the control cabinet model |
Cleaning cloth/vacuum cleaner | Anti-static, dust-free cloth, industrial small vacuum cleaner |
Spare parts kit (provided by the manufacturer) | Folding knives, clamps, fuses, relays, fans, etc. |
5. Summary of key points for panel bender machine maintenance
Maintenance items | Recommended frequency | Description |
Servo system self-check | Weekly | Check whether the alarm is on and the response is abnormal |
Slide rail lubrication | Weekly~Monthly | Use the specified grease |
Tool cleaning and inspection | Per shift/week | Check for wear and cracks |
Control cabinet ventilation system | Monthly | Clean the filter to prevent overheating |
CNC system backup | Monthly~Quarterly | Prevent program loss or misoperation |
Click here to know more about cnc panel benders: