Sheet Metal Cutting Industry Background
The cutting demand for sheet metal cutting industry is constantly increasing, and electrical control boxes, machine casings, and other components in the metal processing industry are generally sheet metal parts. Therefore, the demand for sheet metal processing capabilities is also constantly increasing. As a result, the complexity of the process is also relatively high, and some parts even reach dozens of processes, which also puts higher requirements on precision in sheet metal processing.
Sheet metal processing involves processes such as shearing, punching, and bending, among which the punching process requires a large number of molds, wasting a lot of time and capital costs.
Pain Point:
- I don’t know what kind of cutting equipment is most suitable to me.
- Laser cutting is an efficient and high-quality flexible processing technology. Laser sheet metal processing does not require molds, and compared to traditional processing methods, it is simpler to operate, more flexible, and has lower operating and maintenance costs. The most popular sheet metal cutting equipment nowadays is the laser cutting machine. It is said that one laser cutting machine can solve all sheet metal cutting problems. Is this true?
Sheet Metal Cutting Solution:
Understand the characteristics of various cutting equipment and find the most suitable one.
Metal Sheet Fiber Laser Cutting Machine
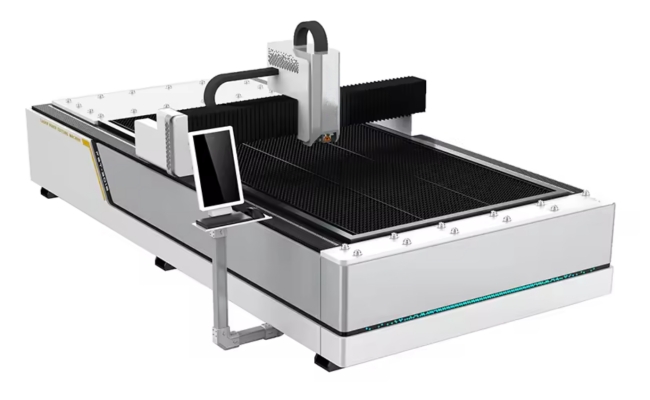
Metal sheet laser cutting machines have various advantages, mainly including:
- High precision and high-quality cutting. Metal sheet fiber laser cutting machine can achieve high-precision processing, not only with high geometric accuracy, but also control cutting dimensions, ensuring smooth and burr free cutting surfaces without the need for subsequent processing steps.
- Fast cutting speed. The laser cutting machine uses a high-speed moving beam to cut the workpiece, which is fast and significantly improves work efficiency.
- High degree of automation. Laser cutting machines are usually equipped with computer control systems, which can automatically complete processing tasks and improve production efficiency.
- Strong adaptability. Sheet laser cutting machines are suitable for processing various materials, including metal, non-metal, and new materials, with a wide range of applications.
- Environmental protection and energy conservation. The laser cutting machine uses a beam of light for cutting, without the need for cutting agents, which is more environmentally friendly than traditional processing methods and can achieve energy-saving effects.
- Low maintenance cost. Laser cutting machines have stable performance, are sturdy and durable, are not easily damaged, and have relatively low maintenance costs in the later stage.
- Reduce material waste. The laser cutting machine has good cutting quality, can save raw materials, and reduce material waste.
- Reduce processing steps. Laser cutting machines can directly produce various hardware workpieces without molds, without the need for manual polishing, optimizing the labor intensity of workers.
- Reduce mold investment. Laser cutting machines can save a lot of mold usage, save processing costs, and lower production costs.
- Reduce environmental pollution. The laser cutting machine operates with low noise, no dust, and does not produce harmful chemicals to the human body and environment, which helps optimize the working environment.
Plate Shearing Machine
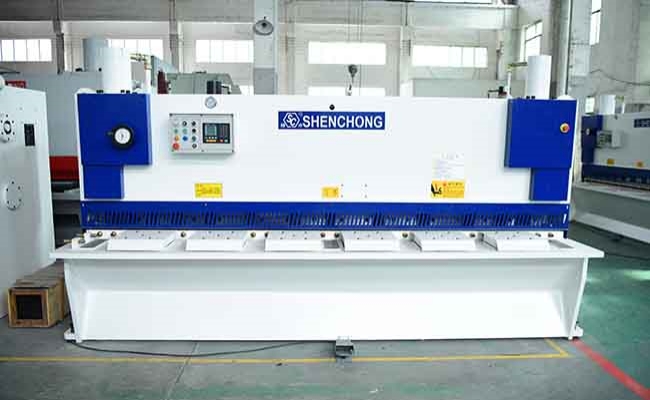
Due to its main linear cutting function, the plate shearing machine can only be used for sheet metal processing that only requires linear cutting. Currently, due to the emergence of laser cutting machines, the market share of plate shearing machines has greatly decreased. However, there are still some cases where sheet metal processing factories can only choose to use hydraulic shearing machines:
- Processing of Large Batch Linear Cutting: In large batch linear cutting, the cutting speed of the plate shearing machine is much higher than that of the laser cutting machine. Therefore, it is recommended to purchase a laser cutting machine in factories that require large batch linear cutting. At the same time, you can also choose to purchase a shearing machine specifically for cutting straight lines.
- High precision: Unlike thermal cutting such as flame cutting, plasma cutting, and laser cutting, shearing machines belong to mechanical cutting, and the stress on the cut sheet is much lower than that of laser cutting machines. Therefore, when customers need ultra-high precision cutting, shearing machines are still more suitable for use.
- Cutting of non-ferrous precious metals: Many precious metals such as cobalt and nickel plates cannot be processed using laser cutting machines, as they will react chemically with thermal energy and cause material deterioration. In this case, only a shearing machine can be used for cutting.
CNC Turret Punching Machine
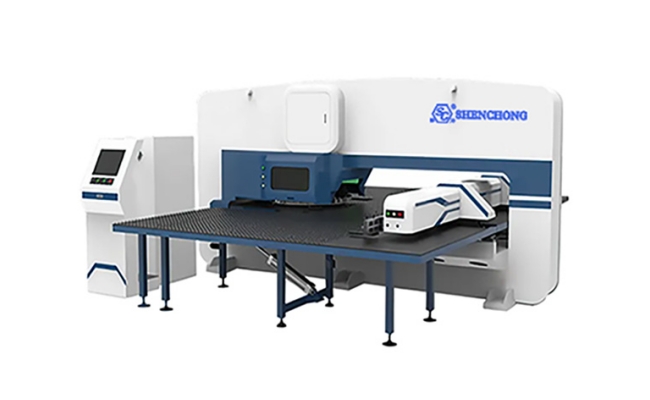
It has limitations on cutting steel plates with a thickness of over 1.5mm, and has poor surface quality, high cost, and high noise, which is not conducive to environmental protection. Due to the high number of burrs on the sheet metal after CNC turret punching and cutting, manual bending can only be selected for subsequent bending, and robot bending cannot be used. At present, the market share of CNC turret punching has been dominated by laser cutting machines. If it is not necessary to punch in large quantities, we recommend purchasing laser cutting machines to replace the function of CNC turret punch press.
Flame Cutting Machine
As the initial traditional cutting method, flame cutting has large thermal deformation, wide cutting seams, wastes materials, and slow processing speed, making it only suitable for rough machining. However, flame cutting has advantages in cutting thick plates. When cutting plates larger than 50mm, the price of flame cutting is much lower than that of laser cutting machines.
Plasma Cutting Machine
The cutting accuracy of plasma cutting is higher than that of flame cutting, but when cutting thin plates, the thermal deformation is larger and the slope is larger. Compared with the precision cutting of fiber laser cutting machines, it is easy to cause waste of raw materials. However, when processing 20mm to 40mm plates, the cost is cheaper than laser cutting machines. However, currently the cutting thickness of laser cutting machines has increased, and the price of laser cutting has decreased. The market share of plasma cutting machines has greatly declined, and more people are considering purchasing fiber laser cutting machines when processing 20-40mm plates.
Waterjet Cutting Machine
High pressure water cutting has a slow processing speed, causes serious pollution, high consumption costs, and is not suitable for sheet metal cutting.